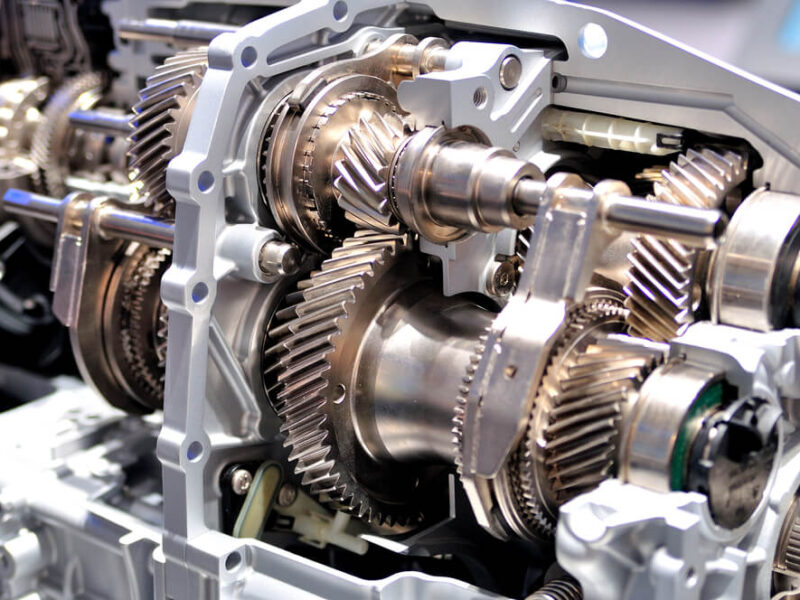
AC motors (alternating current) is a very wide class of motors, including single / multiphase, universal, servo, induction, synchronous, and gearmotor types. The magnetic field, generated by AC motors, is produced by an electromagnet powered by the same AC voltage as the motor coil. The coils that produce the magnetic field are traditionally called the “field coils” while the coils and the solid core that rotates is called the “armature” There are many advantages in the use of ac motors aside from the wide availability of AC power. In general, AC motors cost less than DC motors. Some types of AC motors do not use brushes or commutators. This eliminates many problems of maintenance and wear, and also eliminates the problem of dangerous sparking. They are also particularly well suited for constant-speed applications. This is because its speed is determined by the frequency of the AC voltage applied to the motor terminals.
There are two distinct types of AC motors, synchronous and induction. A synchronous motor consists of a series of three windings in the stator section with a simple rotating area. A current is passed through the coil, generating torque on the coil. Since the current is alternating, the motor will run smoothly only at the frequency of the sine wave. This allows for constant, unvarying speed from no load to full load with no slip.
Induction motors are the more common of the two motor types. They use electric current to induce rotation in the coils rather than supplying the rotation directly. Induction motors use shorted wire loops on a rotating armature and obtain their torque from currents induced in these loops by the changing magnetic field produced in the field coils.
Motion and controls covers a wide range of components that in some way are used to generate and/or control motion. Areas within this category include bearings and bushings, clutches and brakes, controls and drives, drive components, encoders, Integrated motion control, limit switches, linear actuators, linear and rotary motion components, linear position sensing, motors (both AC motors and DC motors), orientation position sensing, pneumatics and pneumatic components, positioning stages, slides and guides, power transmission (mechanical), seals, slip rings, solenoids, springs.
Motors are the devices that provide the actual speed and torque in a drive system. This family includes AC motors (single and multiphase motors, universal, servo motors, induction, synchronous, and gear motor) and DC motor types (brushless, servo motor, and gear motor) as well as linear, stepper and air motors, and motor contactors and starters.
1. Induction
Class of motors that derives its name from the fact that current is induced into the rotor windings without any physical connection with the stator windings (which are directly connected to an AC power supply); adaptable to many different environments and capable of providing considerable power as well as variable speed control. Typically there is “slip,” or loss of exact speed tracking with induction motors.
2. Synchronous
Class of motors that operate at constant speed up to full load. The rotor speed is equal to the speed of the rotating magnetic field of the stator; there is no slip. Reluctance and permanent magnet are the two major types of synchronous motors. A synchronous motor is often used where the exact speed of a motor must be maintained.
3. AC Servo
AC servomotors are typically permanent magnet synchronous motors that can often have low torque-to-inertia ratios for high acceleration ratings.
4. Universal
Class of motor that can operate at approximately the same speed and output on either DC or single-phase AC power; also known as an AC/DC motor.
5. Others –
Unlisted or specialized AC motor construction.
6. Multi-speed
Motor speed can be continuously adjusted or set at discrete speeds within the operating range.
7. Reversible
Motor can be run in both clockwise and counterclockwise directions with approximately the same operating characteristics
1. Induction
Class of motors that derives its name from the fact that current is induced into the rotor windings without any physical connection with the stator windings (which are directly connected to an AC power supply); adaptable to many different environments and capable of providing considerable power as well as variable speed control. Typically there is “slip,” or loss of exact speed tracking with induction motors.
2. Synchronous
Class of motors that operate at constant speed up to full load. The rotor speed is equal to the speed of the rotating magnetic field of the stator; there is no slip. Reluctance and permanent magnet are the two major types of synchronous motors. A synchronous motor is often used where the exact speed of a motor must be maintained.
3. AC Servo
AC servomotors are typically permanent magnet synchronous motors that can often have low torque-to-inertia ratios for high acceleration ratings.
4. Universal
Class of motor that can operate at approximately the same speed and output on either DC or single-phase AC power; also known as an AC/DC motor.
5. Others –
Unlisted or specialized AC motor construction.
6. Multi-speed
Motor speed can be continuously adjusted or set at discrete speeds within the operating range.
7. Reversible
Motor can be run in both clockwise and counterclockwise directions with approximately the same operating characteristics
AC VOLTAGE AND FREQUENCY (Your choices are) | |
1. 115 / 120V 60 Hz 2. 208-230 / 240V, 60 Hz 3. 460 / 480V 60 Hz 4. 575 / 600V 60 Hz 5. 50 Hz / International Power 6. 400 Hz / Aerospace 7. Other | These are standard voltage for 60Hz power (North America). These are for 60Hz power (North America). These are for 60Hz power (North America). These are for 60Hz power (North America). International voltage levels, such as those common in Asia and Europe, and includes all 50Hz power. Motors and other components using 400Hz power are primarily used for aerospace applications. Unlisted voltage / frequency motor. |
ORIENTATION/ TYPE ( Your choices are…) | |
In-line Offset / Parallel Right Angle Hollow Other | Output shaft axis is in-line with axis of motor rotation. Output shaft is parallel with, but not concentric to, the axis of motor rotation. |
DIMENSIONAL DETAILS | |
DESIGN UNITS (Your choices are…) | |
English Metric | It refers to the base units for specifications such as diameter, length, and threading. Combinations are possible and this information is not known for some products. Base units such as inches or fractions of an inch for such primary dimensions as the shaft size, mounting geometry, etc. Base units such as millimeters or centimeters for such primary dimensions as the shaft size, mounting geometry, etc. |
MOTOR SHAPE (Your choices are…) |
Cylindrical Body Square Body | Motor body cross section is round. Motor body cross section is square or rectangular. |
Diameter / Width | Diameter of cylindrical motors or width / height of square motors. This is for the motor body only and does not include flanges. |
Housing Length | Length of motor body, not including shaft. |
NEMA Frame Size | Conforms to a standard size and mounting configuration identified by the National Electrical Manufacturers Association (NEMA). Only numerical sizes are searchable in this field. |
Enclosure Options | (Your choices are…) |
Open Frame / Frameless | Motor with minimal or frame-like support but no overall casing. |
Drip-proof | Drip-proof motors contain ventilation openings that are designed such that drops of liquid or solid particles falling on them from any angle within 15° (degrees) of vertical, cannot enter the motor. |
Dust-proof | Dust-proof motors protect against dust infiltration with features such as total enclosure and labyrinth seals for shafts. |
Totally Enclosed | A totally enclosed motor has an enclosure that prevents free exchange of air between the inside and the outside of the enclosure. Common ratings are TEFC (fan-cooled) and TENV (non-ventilated). It is not an airtight rating. These motors are most frequently used in potentially contaminated environments. |
Special / Extreme Environments (Your choices are…) | |
Clean Room Use Cryogenic Use Explosion-proof Radiation-hardened Vacuum Use | Clean rooms are classified by particulate size and density in the ambient air. One such rating method classifies rooms according to number of particles larger than 0.5 micron in one cubic foot of air; there are various governmental, metric, and international standards. Motors rated for suitability in a clean room will identify the particular standard for which they are rated. Motors with a cryogenic rating are constructed for extremely low ambient temperatures such as 20 K and below. Explosion- proof motors have totally enclosed housings that are constructed to withstand internal explosion of a specified gas, vapor or dust. Should such an explosion occur, the enclosure would prevent the ignition or explosion of the gas or vapor surrounding the motor enclosure. Several explosion-proof ratings are governed by Underwriter’s Laboratories (UL). Radiation -hardened motors are constructed of materials designed to withstand high-energy gamma radiation. Ratings are expressed in units such as permissible RADs in total accumulated dose (TAD). Vacuum-rated motors incorporate features such as lubricant vapor pressure below rated ambient vacuum and construction techniques such as degassing during manufacture to prevent emissions during motor use. |